Oil sludge, an inevitable by-product, is generated wherever exploitation, transportation and refining processes of petroleum industry. It is a complex mixture of petroleum hydrocarbons and water with solid mineral admixture [1]. In China, the growth of oil demand resulted in annual generation of over 110,000 tons of oil field sludge and 800,000 tons of oil storage tank sludge (oil tank sludge) [2]. Both the oil field sludge and the oil tank sludge comprise abundant of toxic substances from the most carcinogenic polycyclic aromatic to heavy metal, and even to radioactive material. Most of them pose the potential risks for human health and the environment. However, at several sites in China, the amount of uncontrolled disposal of oil sludge to the natural environment had reached or even exceeded 20 times of the assimilative capacity of receiving ecosystem. The major sources of oil sludge in this study include the oil field sludge, which is also called hydrocarbon contaminated soil, and the oil storage tank sludge derived from the tank cleaning process.
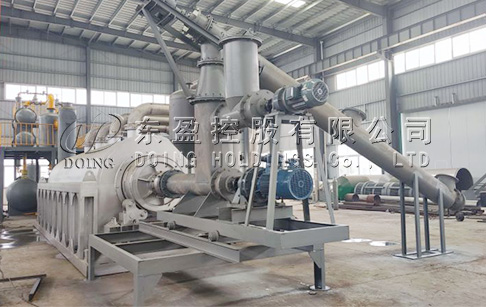
Currently, the most common way to dispose the oil sludge is immobilization and landfill, which requires much space and causes a serious threat to soil and groundwater environment. Biodegradation is considered to be a new and emerging method to decompose the organic compounds in the oil sludge into the lower molecular weight organic compounds. However, due to its unsatisfactory performance on the decompose process of asphaltene composition; this technique remains to be developed.
On the other hand, oil sludge is also a potential recycling resource for its high heating value. So the conversion of the stored energy of oil sludge to various fuel sources for power plants or engines has been recognized as an attractive approach. In this way, after some research, we recommend the fully automatic continuous oil sludge processing plant with the continuous feeding and slagging process, which could process the waste continuously without stop.
The advantages of the continuous oil sludge processing plant
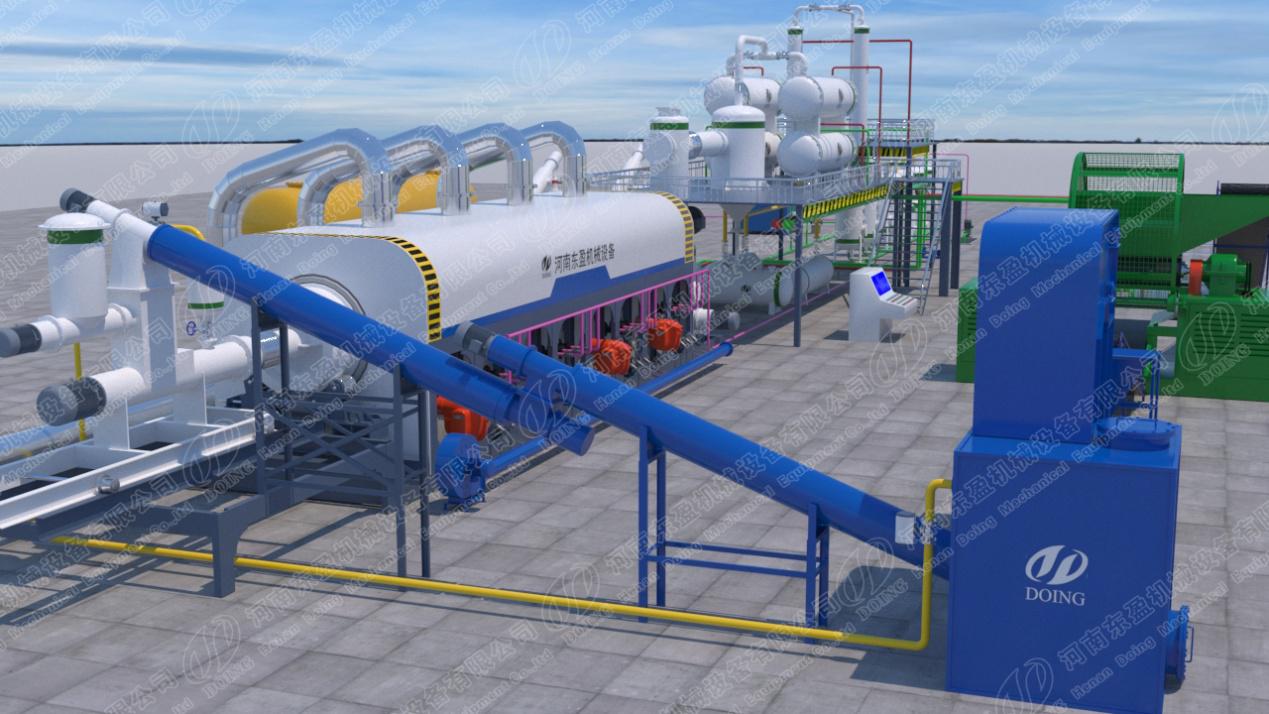
1) The new type continuous oil sludge processing plant adapts rotated reactor, which could be heated evenly in 360°. This way it would not heat only one part of the reactor for long time, thus to make the reactor more durable.
2) Inside the reactor, there is the rollover device. The input materials would be turned over 4000 times from feeding to slagging. And the materials inside the reactor are forced to be turned over continuously and highly dispersed, which could get evenly heating , thus greatly increase the pyrolysis speed.
3) To adapt rotation outside and inner diverter heating method, the raw materials is pyrolyzed against the wall of reactor by directly touching the heat transferred reactor surface of the continuous oil sludge processing plant. To receive heat fast to make sure that the heat exchange is fast.
4) The capacity of continuous oil sludge processing plant can be adjusted. Multiple reactors can be connected in parallel to achieve big scale production. Our reactors can be increased or decreased according to our clients’ production demand, thus we can adjust the production scale. Besides, the single reactor with smaller size is more easy and convenient for delivery in containers and assembly in clients’ factory. If our clients do not want to assemble multiple reactors, every single reactor can also work separately to combine big capacity.
Referenced specifications of continuous oil sludge processing plant
Item |
Reference |
|
1 |
Working method |
Fully continuous process without stop 24/7 |
2 |
Reactor Structure |
Horizontaltype, external rotating reactor, input material moved inside reactor through a guiding device. |
3 |
Reactor size |
According to capacity |
4 |
Electricity consumption |
50 KW/H |
5 |
Heating method |
Indirect heating, no direct fire to reactor |
6 |
Heating resource |
Any fuel oil or gas, with the recycled tail gas |
7 |
Cooling method |
Circulation water |
8 |
Sealing |
Both hard and soft sealing. Mainly use soft sealing. |
9 |
Control method |
Intelligent, variable frequency automatic control +manual operation: also can be made full PLC system without any manual control according to customer requirement |
10 |
Area |
Around 1000m² normally |
11 |
Application |
Solid waste treatment |
12 |
Reactor material |
Q245R boiler plate (stainless steel as optional) |
13 |
Machine life |
5-15 years according to actual operation |

